Tank Welding Inspection: Ensuring Long-Term Resilience and Safety
The Crucial Function of Container Welding Assessment in Ensuring Structural Integrity and Security Conformity in Industrial Applications
In the realm of commercial applications, tank welding inspection emerges as a pivotal aspect in safeguarding structural honesty and making certain conformity with safety guidelines. Using a combination of techniques such as aesthetic evaluations and progressed testing methods, these assessments offer to recognize and alleviate possible problems before they escalate into significant threats.
Significance of Tank Welding Evaluation
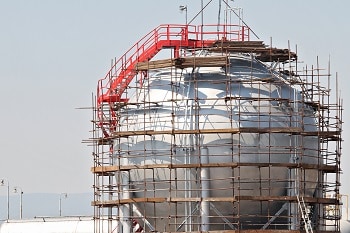
Guaranteeing compliance with sector standards and laws is an additional substantial facet of tank welding assessment. Regulatory bodies mandate strict guidelines for the building and upkeep of storage containers, and comprehensive examinations assist companies follow these needs. Non-compliance can result in extreme penalties, including penalties and shutdowns, better highlighting the need for rigorous assessment protocols.
Moreover, tank welding inspection plays an essential duty in maintaining functional effectiveness. Routine assessments can identify potential concerns prior to they intensify, facilitating timely fixings and decreasing downtime. This positive approach not only enhances safety yet additionally contributes to set you back savings over time. In recap, the relevance of container welding assessment depends on its capacity to protect public health, safeguard the atmosphere, and guarantee conformity with governing frameworks.
Key Examination Strategies
Reliable storage tank welding inspection counts on a range of vital strategies that make sure detailed analysis of weld top quality and structural honesty. Amongst one of the most prevalent techniques are aesthetic evaluation, ultrasonic testing, radiographic screening, and magnetic particle testing - Tank Welding Inspection. Each technique supplies distinct benefits in assessing different facets of the weld
Visual examination functions as the first line of protection, permitting examiners to determine surface area defects, abnormalities, or incongruities in the weld bead. Ultrasonic screening employs high-frequency acoustic waves to spot interior imperfections, such as fractures or voids, offering an extensive assessment of weld stability. This approach is specifically reliable in discovering concerns that may not be noticeable on the surface area.
Radiographic screening makes use of X-rays or gamma rays to generate photos of the welds, disclosing interior interruptions and providing a permanent document for future recommendation. This method is extremely efficient for important applications where the threat of failure have to be lessened.
Last but not least, magnetic fragment screening is utilized to determine surface and near-surface problems in ferromagnetic products. By applying electromagnetic fields and great iron fragments, examiners can identify gaps that may compromise the structural stability of the tank. With each other, these strategies create a robust framework for guaranteeing high-quality welds in commercial applications.
Compliance With Safety And Security Requirements

Routine inspections play an essential function in making sure conformity by determining potential failures or deviations from suggested criteria. Inspectors are trained to examine weld high quality, confirm material requirements, and evaluate the general structural honesty of storage tanks. Their experience is vital in guaranteeing that welding processes satisfy the needed safety standards.
Additionally, compliance with security criteria not just shields workers however likewise safeguards the atmosphere from prospective threats such as leaks or devastating failings. Organizations that prioritize safety compliance are better placed to minimize dangers, boost operational efficiency, and foster a society of security within their labor force. In recap, maintaining strenuous conformity with safety standards is essential for the successful operation of container welding activities in commercial settings.
Advantages of Routine Examinations
Normal evaluations are integral to maintaining the structural honesty and security of welded storage tanks. These inspections provide a systematic strategy to recognizing potential flaws or weaknesses in the welds, guaranteeing that any issues are addressed before they intensify into considerable failings. By performing regular evaluations, organizations can identify deterioration, tiredness, and various other forms of wear and tear that might jeopardize storage tank performance.
Moreover, regular inspections add to compliance with industry policies and standards. Sticking to these standards not just reduces lawful dangers but likewise improves the company's online reputation for security and integrity. Normal examinations foster a proactive safety culture, encouraging workers to identify and focus on the relevance of devices integrity.
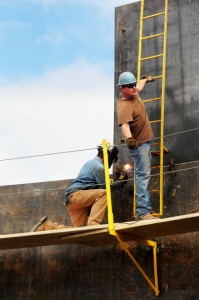
Study and Real-World Applications
Instance researches and real-world applications show the concrete effect of effective storage tank welding evaluation practices. visit here Following the execution of strenuous welding examination procedures, including aesthetic and ultrasonic screening, the center determined crucial defects in weld joints that could have led to disastrous failures.
Likewise, a water therapy plant implemented a thorough assessment program for its storage tank welding procedures - Tank Welding Inspection. By integrating non-destructive testing approaches, the plant had the ability to find early indications of rust and exhaustion in weld joints. This prompt intervention expanded the life-span of the tanks and made sure compliance with safety and security guidelines, thus safeguarding public health and wellness
These study underscore use this link the relevance of routine and systematic container welding assessments. By prioritizing these practices, markets can alleviate dangers, enhance structural integrity, and guarantee compliance with safety criteria, inevitably leading to improved functional effectiveness and minimized liabilities.

Verdict
In final thought, container welding examination is a crucial part of maintaining structural integrity and safety in industrial applications. Utilizing numerous assessment methods ensures early discovery of potential problems, therefore preventing tragic failings.